Senior design projects have been a long-standing tradition for engineering and computing students at Gannon. Students’ final years are a culmination of the skills and knowledge they’ve learned to design, build and present a created product or service.
This tradition was enhanced to advance the College of Engineering and Business’ focus on cross-disciplinary learning, integrating entrepreneurial thinking and career preparation.
“Developing an entrepreneurial mindset is one of our goals,” said Karinna Vernaza, Ph.D., dean of the College of Engineering and Business. “During the 2018-19 academic year, we intentionally started providing opportunities and projects that were cross-disciplinary to model the nature of products and processes in industry. Our students are able to experience and understand the importance of bridging fields of study to create a viable and marketable product or process.”
Students and advisers from a sample of this year’s projects have provided first-hand accounts of their learning journeys.
Capturing Micro- and Meso-Plastics
Project Summary: Create a solar-powered active system to remove micro- and meso-plastics from water bodies in high-density, urban areas.
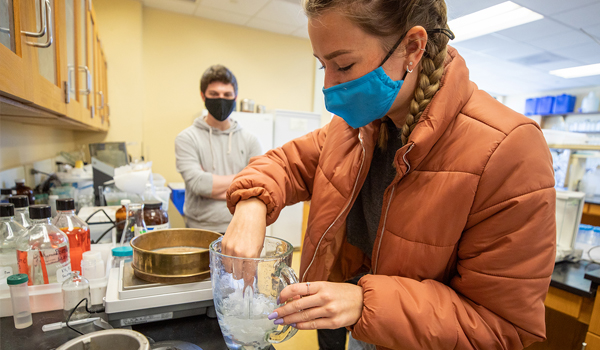
Students
- Olivia Graham ’21, environmental engineering
- Alexa Howard ’21, environmental engineering
- Zachary Mansour ’21, electrical and computer engineering
- Arvin Sharifbaev ’21, mechanical engineering
Adviser
- Varun Kasaraneni, Ph.D., assistant professor of environmental science and engineering
The students had the same goal in mind when they selected this project that stems from their adviser’s research: to be part of something that makes a difference.
“After climate change, plastic pollution is a major environmental issue that needs to be solved,” Kasaraneni said. While technology exists to remove large plastic items from water, not much has been created for micro- and meso-plastics. Students’ design allows the system to remain in the water until maintenance is needed, making the technology a unique prototype for large-scale efforts in Presque Isle and elsewhere.
“If we can create an active system, you can scale this project up and remove more micro-plastics to make a difference. This isn’t a thing people are doing yet,” Mansour said.
The students designed an eco-friendly and sustainable system using 3D-printed parts, solar panels, electrical units, a clarifier and flotation device. Through trial and error, they brought together a final design that was lab tested in May and will be tested in Lake Erie once the system is completed.
“The interdisciplinary work is a huge factor,” Mansour said. “In the world we live in, you can’t make something without working with other engineering disciplines.”
“This is why I went into the field,” Howard said. “I want to do good for the environment. It has been fulfilling that I’ve been able to do this at college.”
Simulating Flight to Improve Ergonomics
Project Summary: Design an interactive aircraft simulator to improve pilot ergonomics using sensors, actuators and virtual reality projection built within a helicopter frame on a Stewart platform.
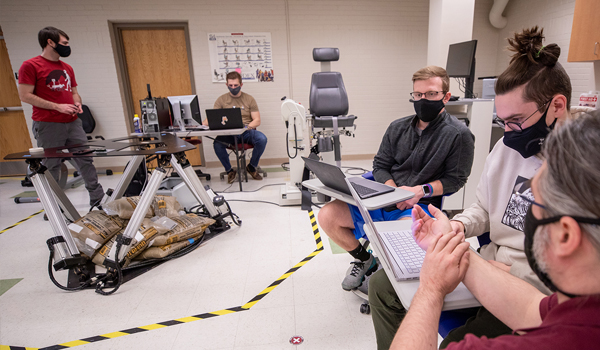
Students
- Connor Byers ’21, industrial and robotics engineering
- Kaden Conley ’21, biomedical engineering
- Mike Eckels ’21, electrical engineering
- Keefer Gregoire ’21, electrical and computer engineering
Advisers
- Xiaoxu Ji, Ph.D., assistant professor of biomedical engineering
- Davide Piovesan, Ph.D., associate professor of biomedical engineering
- Yong-Kyu Jung, Ph.D., associate professor of electrical and computer engineering
Students brought their expertise together to build a safe aircraft simulator using a life-size helicopter frame previously donated to the University. The students expanded on the helicopter's research possibilities to assess ergonomic impact on its operator. This is a task that many vehicle and machinery manufacturers use in the real world to improve their operations and optimize product safety for the pilot or driver.
The students designed one integrated system that combined virtual reality with a platform that models the range of motion one would experience while operating an aircraft. They used their skills in software and circuit design to write and optimize algorithms to interface with the user-friendly Microsoft Flight Simulator, as well as experience with motion-capture and industry-grade software.
“Working with different types of engineers has helped build the relationship to understand what they have to do and how that’s important to the things I have to do,” Conley said. “I’m working on a real-life project and this work that I’m doing can be used down the line ... It’s a surreal moment for me.”
“I’m working on a real-life project and this work that I’m doing can be used down the line ... It’s a surreal moment for me.” - Kaden Conley '21
Designing Prosthetics to Increase Quality of Life
Project Summary: Develop a prosthetic system designed specifically for a dog who lost both rear legs using broad veterinary prosthetic concepts.
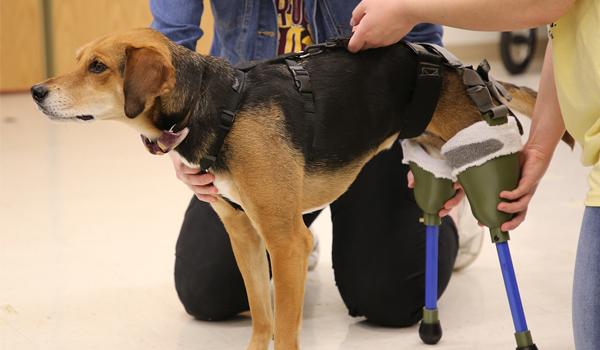
Students
- Julia Baumgarner ’21, biomedical engineering
- Samantha Moretti ’21, biomedical engineering/mechanical engineering
- Emily Schweitzer ’21, biomedical engineering/mechanical engineering
- Noah Cardella ’21, mechanical engineering
Adviser
- Scott Steinbrink, Ph.D., associate professor of mechanical engineering
When Schweitzer attended a Joey’s P.A.W. charity event two years ago, she did not realize the connection she made that day would come full circle into her academic experience to improve the life of a dog named Boone.
Joey’s P.A.W. raises money for special needs dogs to provide prosthetics and wheelchairs and helps those dogs become adopted. Boone came to the charity after his hind legs were severed from abuse. He was adopted by the charity owners, Charlie and Tanya Diable (pictured left).
Schweitzer knew she wanted to develop prosthetics when it came time to select her senior design project. “What if we develop prosthetics for a dog in need?” she thought.
The students worked closely with their adviser and the Diables to learn more about Boone’s needs, finding he had already tried several prosthetics unsuccessfully.
They evaluated all aspects of the prosthetic, from the structure to the materials to ensure it was best for Boone.
They created several iterations of product design using laser scanning, CAD software and several 3D printers, including a Polyjet printer for the rubber feet and carbon fiber printers for the adjustable pylon that acts as the leg.
The students realized their work was twofold: gaining valuable experience to prepare them for their careers making a difference in the life of a dog in need.
“The support shown from the people following this project and our professors has been absolutely amazing,” Cardella said. “It adds a dimension on the emotional side when we know our project will change a life. It helped us strive to create the absolute best solution we can to help Boone.”